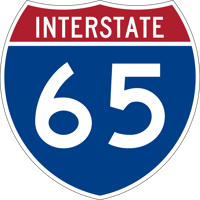
I-65 Project
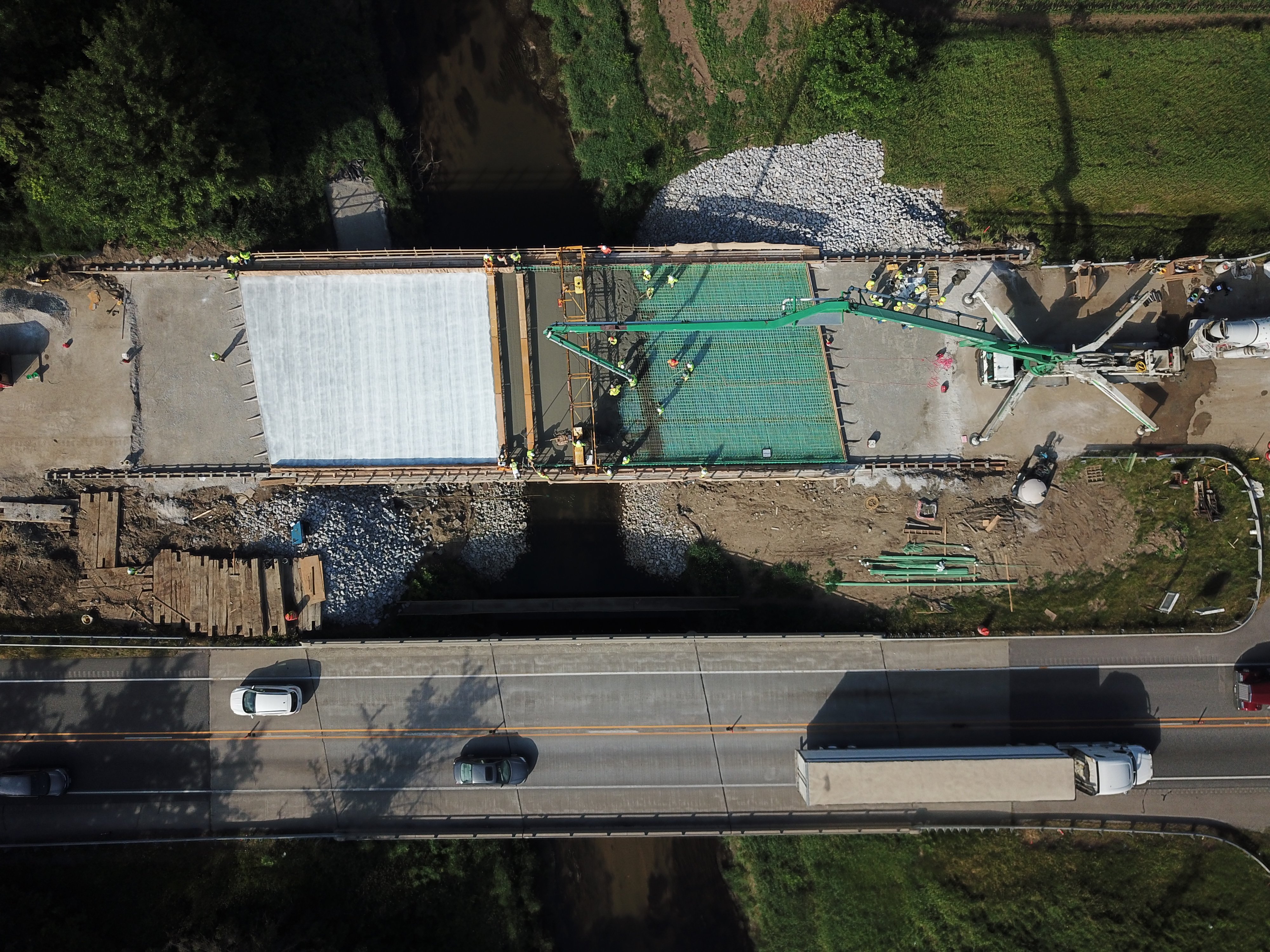
Industry
Highway System
Challenge
The project encountered key technical hurdles, including high early-age shrinkage cracking, inefficiencies due to multi-step concrete finishing procedures, extended curing requirements, and elevated material consumption, particularly in cement and supplementary cementitious materials (SCMs). These factors collectively impacted structural performance, labor productivity, and scheduling.
Results
Implementation of a next-generation nano-silica admixture provided measurable performance improvements. Cracking was reduced by 70%, mitigating long-term durability concerns. The admixture allowed the consolidation of a previously two-step process into a single-stage placement and finishing operation, increasing operational efficiency. Additionally, the admixture eliminated the need for wet curing and curing compounds, simplifying field operations and reducing labor demands. The optimized mix design enabled a 15% reduction in cement and SCM usage, contributing to lower material costs and a reduced carbon footprint. Overall, the solution substantially accelerated project delivery timelines without compromising quality or performance.
Key Products
E5® Internal Cure, E5® Liquid Fly Ash
E5® INTERNAL CURE AND E5® LIQUIDFLY ASH OVERCOME WINTER WEATHER CHALLENGES, CONCRETE MIX DESIGN LIMITATIONS, LABOR, AND SUPPLY CHAIN SHORTAGES, SAVING LANDMARK INFRASTRUCTURE CONSTRUCTION SCHEDULE & BUDGET
Indiana
DOT
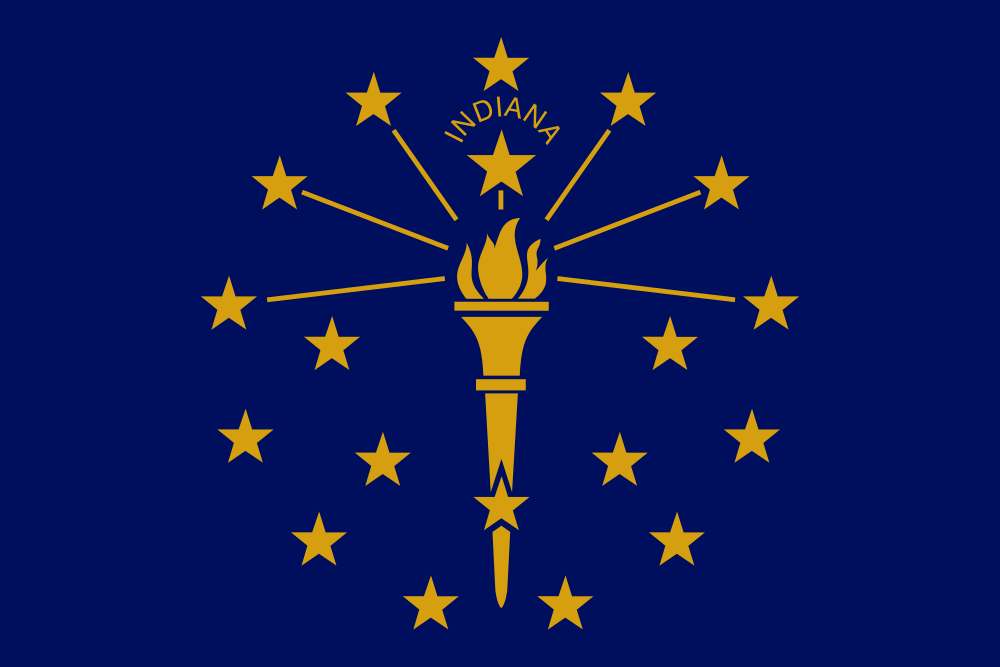
About Indiana and I-65
Indiana is a Midwest U.S. state known for its agriculture, manufacturing, and the iconic Indianapolis 500. Its central location makes it a key hub for transportation and logistics. Interstate 65 runs through the state from Gary to Indianapolis, continuing south to Mobile, Alabama. As a major north-south route, I-65 connects Indiana to key cities and plays a vital role in commerce and travel across the region.
Project Overview
The project team faced multiple concrete performance and construction sequencing challenges that threatened to impact both schedule and durability. Early-age cracking posed a significant risk to structural integrity and long-term performance. In addition, the concrete placement process required a two-step finishing approach that increased labor demands and introduced opportunities for inconsistency. The curing process further complicated scheduling, as it relied on time-intensive wet curing and the application of chemical curing compounds. Compounding these challenges was the high volume of cement and supplementary cementitious materials (SCMs) required to meet strength and durability targets, which added cost and increased the carbon footprint of the project.
How E5 Elevated Performance
E5® Nano Silica admixtures give control back to the finishing crews and accelerate construction schedules. E5® Nano Silica eliminates hardeners, sealers, and curing compounds. When used as a system, E5® provides internal curing, extremely high abrasion resistance and high FF/FL levels. Crews gain access to the slab much quicker than compared to topically treated slabs.